Main process and principle:
Choose the organic solvent that can dissolve the oil, through contact with the oil
materials(steep or spray), to extract the oil out from the oil-bearing materials.
Processing: steeping the oil flake/cake into the solvent, get the miscella, separating the miscella and solid residue(meal), then after evaporating, stripping according to the different boiling point, the solvent will turn gas separate with the oil, then get the extract crude oil. The solvent will be cooling and recycle. There will be some solvent in the meal, after desolventizing, drying, can get the dry meal, the solvent will also recycle after cooling.
This equipment suitable for soybean, cottonseed, rapeseed, corn embryo, rice bran and so on. For the low oil content oil materials, generally adopt extruding-extracting technology, which technology can destroy the oil cell structure, passivating the enzymes and this kind of poisonous element, make the flake extruding, enlarge the contact area with the solvent, favorable for the oil extraction.
For the high oil content oil materials, adopt pre-press and extraction technology. It can get some oil from pre-press procedure, then extractiong the oil cake after pressed, to enhance the efficiency of extraction.
This equipment is continue complete extraction equipment, compose of extracting, wet meal roasting desolventizing, miscella treatment, solvent condensation recovery four parts. It’s mainly made up of extractor,desolventing machine,long pipe evaporator,discal stripper, condenser and other equipment,and it’s matched with explosionproof motor,various kinds of connected pipes in plant,as well as the required accessories of instrument,apparatus,valve and so on.
Main extraction technology:
Batch extraction
For the process of oil flake coming into extractor, meal unloading from the extractor, the injecting of fresh solvent and extracting of miscella all is for batch, discontinuous and periodic. It mainly applicable to small scale oil mill using. The main equipment is extractor, condenser, long pipe evaporator, stripping tower, absorption tower and so on.
Suitable capacity: 1-20ton/day, especially for rare oil materials and valuable oil extracting.
Main data
Capacity: 3 - 10 tons/day
Operator: 4-6 persons/shift
Residue oil of meal < 2.0%
Residue solvent in meal < 700 ppm
Consumption (kg/t raw materials)
Steam < 500; Solvent < 6; Electricity < 25kw.h; Water(recycling water) < 50
Continuous extraction
Include rotocel extractor type, loop type extractor and so on.
It's all for continuous for the process of oil flake coming into extractor, meal unloading from extractor, fresh solvent injecting and miscella extracting, mainly contain the below four work procedure:
Rotocel extractor loop type extractor
Extract technology:
The flake/cake come from the pre-treatment/pre-press plant, convey to the materials silo by drawing template conveyer. There is one cone-shaped off valve type feeder in the bottom of materials silo, the spool of the feeder match up with the materials level, automatically control the materials height, to prevent the solvent gas countermarch to pre-treatment plant.The oil flake/cake enter into the extracting cell of the extractor, under the slow move of rotor,the oil flake/cake sprayed and immerse by miscella with different consistence, finally sprayed and immerse by the fresh solvent, they are refluent. The circulation of miscella is finished by miscella circulating pump. The oil materials after extracting discharge into meal silo after draining. The meal discharger device equip the cylinder meal discharge equipment with two outdevice, which better solve the crosslink problem of meal silo also buffering wet meal's strike effect to the drawing template. The wet meal enter into the desolventizer-toaster by drawing template. The dense miscella pumped enter into the miscella treatment process through miscella oil filter. Generally the height of materials in rotocel extractor is 2-3m, extracting time is 90-120 minutes, extracting temperature is 50-55ºC, the solvent content in wet meal is less 30%, the concentration of miscella is 20-25%.
Wet meal roasting-desolventizing process
The wet meal convey by drawing temple conveyer to DTDC desolventizer-toaster,which normally 9-10 layers, the top 1-3 layer is pre-heat layer, 4-6 roasting layer, 7 for directly steam roasting-desolventizing layer, 8-10 for hot air drying and cold air cooling layer. After roasting-desolventizing, drying, cooling treatment, the solvent content in finished product meal is less 700ppm, water content less 12%, meal temperature is 40ºC or so. The finished product meal convey by drawing temple conveyer to meal storage, after metering, packing, then store. The mixed steam come from desolventizer-toaster as the hot source enters into the 1st evaporator after catch meal powder using solvent by moisture drip catcher. The exhaust gas from 8-10 layer expel to the air, meal power enters into finished product meal drawing template conveyer.
Miscella treatment process
The dense miscella coming from the extractor after separating by miscella filter enters into miscella vessel where for further sedimentation, separation, pump into the 1st long pipe evaporator. The hot source of 1st evaporator comes from the second steam of desolvenizer-toaster and the heating steam of steam vacuum pump. The miscella after the 1st evaporating and separating of gas and liquid pumped into cold-hot oil exchanger, after heating, enters into the 2nd long pipe evaporator, after second time evaporating and separating then pumped into the stripping column, the miscella expel from stripping column which slovent content below 500ppm, temperature for 105ºC or so pumped into heat exchanger, send to the refining plant after cooling. The negative pressure of miscella evaporating and stripping system is shaped by vacuum pump.
Solvent recovery process
The mixed steam expel from the desolventizer-toaster after used as the hot source of the 1st evaporator, the condensate enters into water separator, the other steam didn't cooling come into economizer, injected by condensate in condenser, condensate enters into water separator, the steam didn't cooling go to desolventizer-toaster condenser for cooling then also enters into water separator. The mixed steam and solvent steam come from the 1st and 2nd evaporator all enter into evaporating condenser. The vacuum pump made the negative pressure of the condenser then the evaporator. The mixed steam come from stripping column enters stripping condenser for cooling, condensate expel into water separator, the gas didn't cooling pumped out by vacuum pump enters into the 1st evaporator, cause the stripping condenser and stripping column for negative pressure. The free gas in extractor after cooling by extractor condenser, the condensate enters into water separator. The free gas comes from desolventizer-toaster condenser, extractor condenser, water separator, solvent storage enters into the last condenser, condensate discharge into water separator, the gas didn't cooling enter into mineral oil absorption column, in which the solvent steam absorb by cold paraffin oil, the air didn't absorbed and very few solvent gas expel to the air by the fan in top of the tower. The cold paraffin oil with solvent heated by heat exchanger and heater, enter into desorption column for steam stripping, desorb out the solvent separated from the paraffin oil, the mixed steam expel from the desorption column enters into evaporate condenser. The solvent separated from water separator enters into solvent turnover storage, then boiling the water separated out, recover the residual solvent then discharge the water through water seal tank. The solvent in solvent turnover storage pumped out, heating by solvent pre-heater and then enters into the extractor for recycling.
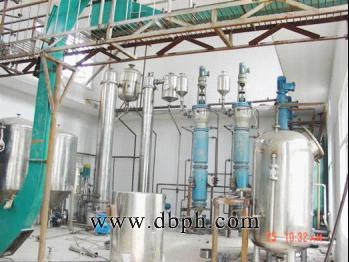
one corner of extraction plant
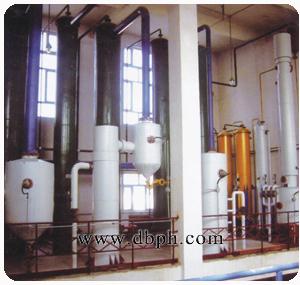
cooling part paraffins vent gas recovery
Main data
Capacity: 10 - 1000 tons/day
Operator: 2-4 persons/shift
Residue oil of meal < 1.0%
Residue solvent in meal < 300 ppm
Consumption (kg/t raw materials)
Steam < 300; Solvent < 1.0; Electricity < 15kw.h; Water (recycling water) < 30
Flowchart:
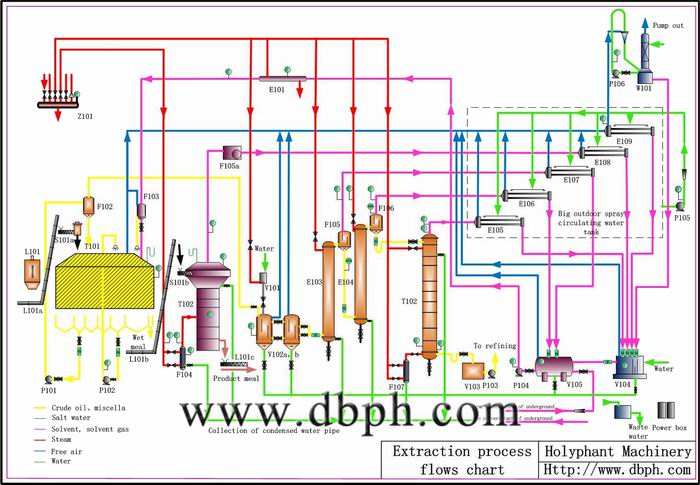